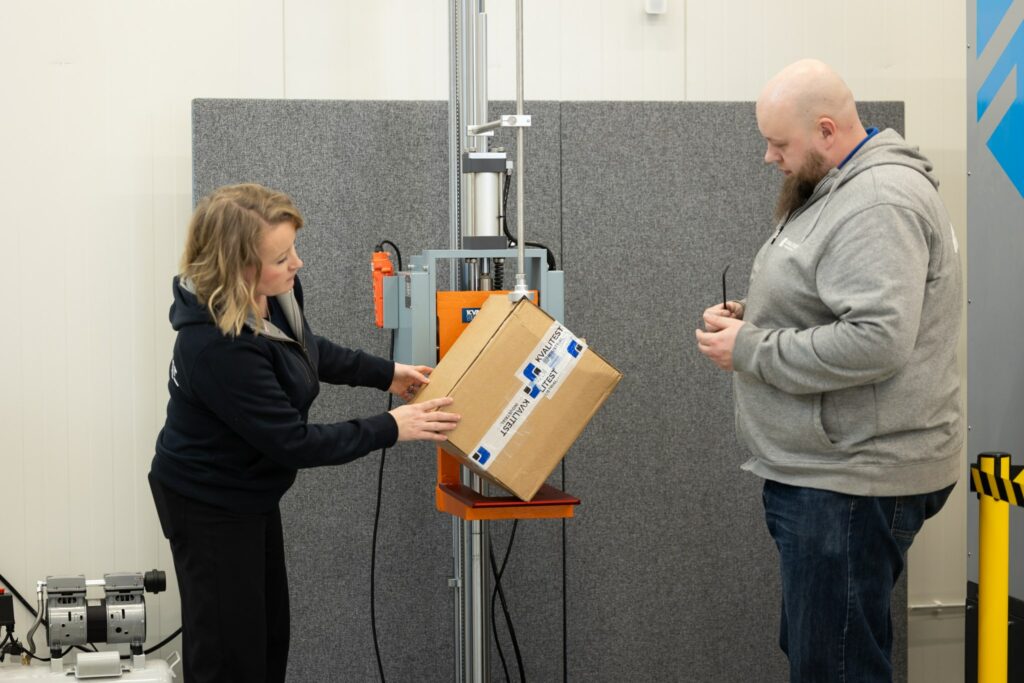
What are the most common causes of packaging damage and how can you prepare for them?
Drops and impacts in transport environment
A shock is a short-duration, high-intensity event, often caused by a sudden change in velocity, such as when a moving object stops abruptly. For packaging, common examples include drops. Effective packaging must withstand these shocks throughout the distribution route. Falling and impact hazards are everywhere in the transport chain. Therefore, identifying them and knowing the transport environment is very important.
Shocks and impacts during transport
Packages are dropped or hit several times during distribution, but most drop heights are quite low. The majority of drops occur during packaging handling, or when transferring to or from a vehicle.
Handling situations, including sorting, loading, unloading, and transferring packages between vehicles, present numerous opportunities for drops, exposing packages to fall hazards.
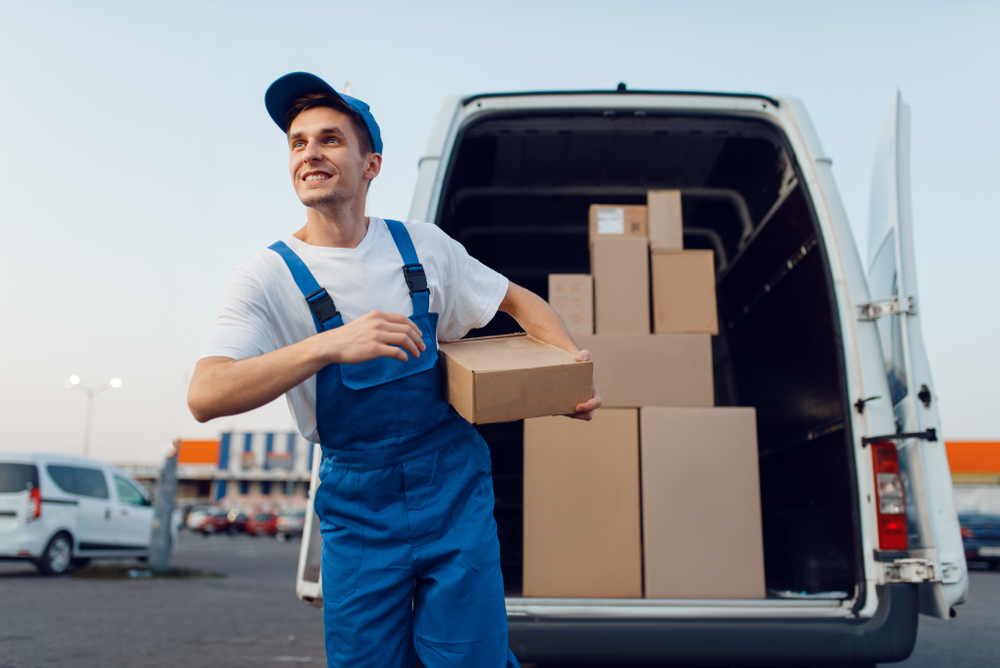
Mechanical processing of packaging
Drops can happen accidentally or they can be intentional. They can be caused by e.g. from human clumsiness or carelessness, slipping, etc. Accidental falls occur relatively rarely, but in such cases the height of the fall is often high, and the direction of the fall may change upon impact.
Haste is also poison for packaging: especially during high season, damage losses increase when shipment volumes increase and personnel have to be stretched beyond their usual operating capacity. Sometimes the shock faced by the package is due to the lack of proper handling equipment or facilities.
The efficiency mindset exposes to drops
Often, efficiency drives handling practices that increase drop risks. For example, dropping, kicking or throwing packages into place is faster than careful placement, making low-height drops common during everyday activities.
When thrown, the package can travel a long distance with a net effect at the end of the drop. These events can be damaging to both the package and the product inside it. In addition, the surface against which the package falls or hits affects the strength of the impact on the product. Packages are also routinely dropped on top of other packages. These handling shocks are typically short in duration and high in acceleration.
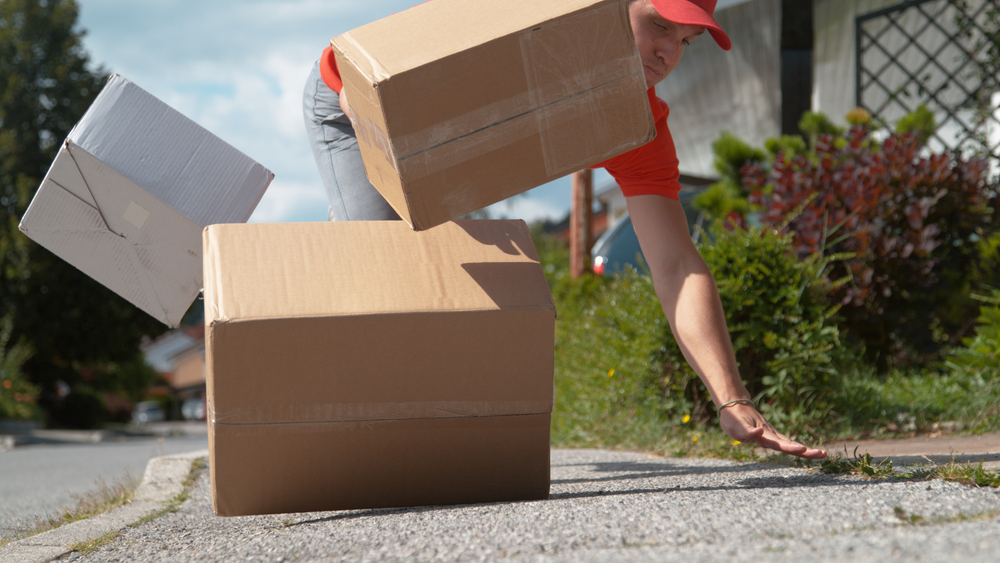
Not so nice scenarios. How can you prepare for these or how can you protect yourself from damage?
To mitigate these risks, effective preparation and protective measures are crucial. One of the most effective strategies is through careful testing, such as drop testing, to evaluate and improve packaging resilience.
Affordable and sensible testing with drop testing equipment
Drop testing is a common and effective method for validating packaging’s resilience to transport stresses. It’s affordable, requires minimal training and provides valuable, repeatable data to improve packaging designs.
The drop tester you get yourself pays for itself very quickly, and you can perform and repeat tests almost endlessly in your own laboratory. Here you can use your own methods and ready-made test standards, for example ISTA methods, which have several alternative ways to produce shocks.
Repeatable, reliable and correct information
All development work is built around repeatability. If the testing is not repeatable, it is also not comparable. And as we know, data is power. Therefore, comparable and valid drop data should be obtained with a drop tester developed for that purpose.
Why is dropping from the arm not suitable? Such tests are usually not sufficiently precise, controllable or repeatable. Setting them up is time-consuming and prone to inaccuracies. Instead of tape and string tunings, you should choose a drop mechanism developed for this purpose, which is most commonly a drop tester. The mechanism of the tester makes controlling the packaging direction easy and repeatable. The drop tray swings out from underneath super fast, allowing the package to fall freely onto the test tray. The direction of the drop (for example, the corner, edge or side of the package) is usually defined in the test standards.
Free-falling testers are used for testing small and medium-sized packages. The packages are tested by dropping the package freely onto a hard surface, usually a steel plate. They can also be dropped on top of another package or on an object such as a wooden block.
In conclusion
✅ While testing according to standards doesn’t eliminate all transport risks, it significantly strengthens your position in potential disputes by demonstrating due diligence in assessing and mitigating packaging vulnerabilities.
You can find out about package testers and equipment here.